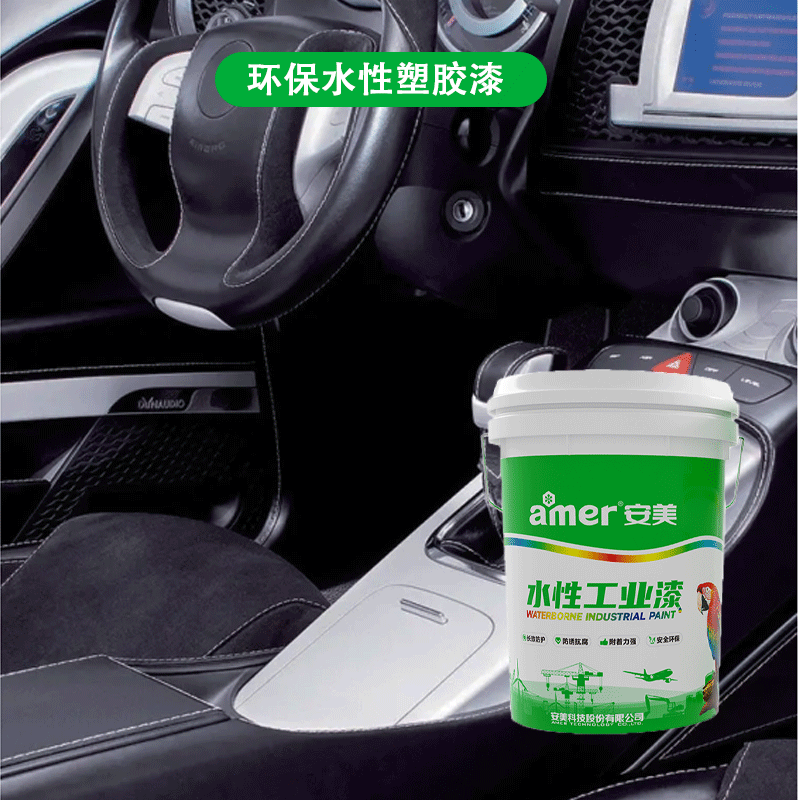
环保水性塑胶专用漆
安美环保水性塑胶漆由国内前治研发团队倾力打造,产品广泛应用在3C电子产品、智能家居、智能家电、移动穿戴、汽车、摩托车、运动器城等塑胶外壳的涂饰上,以绿色环保、节省成本、极致性能、方便施工等特性,可为客户灵活提供定制化解决方案,成为客户的理想之选。
发布者: 发布日期: 阅读量:2589次
铰孔是精加工孔的方法之一,在实际生产中应用很广,特别是对于较小的孔径,相对于内圆磨削及精镗而言,铰孔是一种较为经济实用的加工方法,可以通过铰刀从工件孔壁上切除微量多余材料,提高其形状位置精度和表面粗糙度。
切削冷却液厂家在长期的生产实践中认识到,除了通常关注的设备和加工参数之外,在切削液的使用方面,选择不同的切削冷却液种类、采用不同的切削液浓度、切削液的清洁与否以及温度的变化等,都会对铰孔质量产生一定的影响。
切削液的选择目前常用的切削液大致分为三类:水溶液、乳化液和切削油。不同的金属材料其力学性能和工艺性能存在一定的差异性,所以铰孔时,厂家必须根据加工对象的不同性能特点,选择使用合适的切削液。
铰削中碳钢和合金钢时,由于中碳钢和合金钢有良好的切削加工性能,加工时不会产生大量的切削热,切屑易变形折断,刀具不易磨损,所以选择切削液时,主要采用以润滑为主、冷却为辅的切削液,以达到减小工件的表面粗糙度的目的。
低速铰孔时,宜选浓度大的硫化乳化液;中速铰削时,宜选用硫化油与煤油的混合液,增加润滑性。
铰削不锈钢时,由于不锈钢材料的导热性差、切屑易粘刀、刀具磨损快等特点,选用切削液要以降低温度、清洗切屑为主。将3%的*加2%的碳酸钠用少量热水混合,然后将1%的L-AN46全损耗系统用油加0.5%的乙醇合于一起后用余量的水稀释,这样配成的乳化油铰削不锈钢效果很好。
铰削铸铁时,由于铸铁中石墨的存在对基体有割裂作用,所以铸铁的强度、塑性和韧性很差,但硬度和脆性很大,且表面有细小的裂纹和针孔,加工中易形成崩碎切屑,不需要冷却,润滑效果也不明显,因此,铰铸铁孔时,不加切削液,如能一孔重复铰削两遍,可减小工件的表面粗糙度值,使工件表面粗糙度值减小到Ra3.2mm左右。
铰削黄铜时,由于黄铜由铜和锌元素组成,工业中一般采用的黄铜含锌量不超过45%,故其特点是塑性好、强度高以及切削加工性好,加工时需加以润滑作用为主的切削液,一般用粘度较大的菜油。
铰削生铝,即铸造铝合金时,由于此类合金的塑性差、强度低且脆性大,加工时表面粗糙度值大,铰削时加煤油或30%煤油与70%菜油的混合油能减小工件的表面粗糙度值。